Keeping the country moving calls on a wealth of skills from manufacturing to end-of-life recovery. BTMA is active in providing up-to-date guidance to industry professionals on a wide range of tyre-related topics.
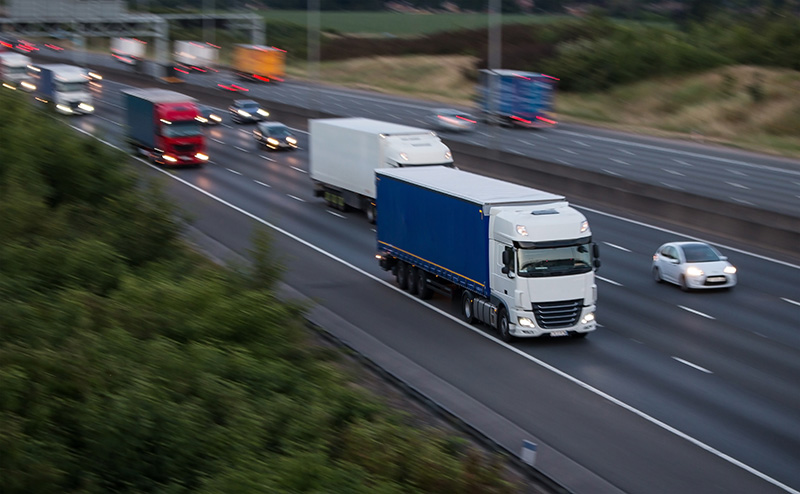
Technical Guidance for minor repairs to tyres for cars and light commercial vehicles
Some minor damage to car or light van tyres can be safely repaired; principally punctures to the central area of the tread that are less than 6mm in diameter. Repairs to the sidewalls, other than for cosmetic damage, may not assure the structural integrity of the tyre and are not approved. In all cases tyre repairs should be carried out by a trained and competent operator.
BTMA only condones tyre repairs which are carried out in accordance with the recommendations in the prevailing issue of British Standard BS AU 159, currently suffix g. Before commencement, consumers are advised to confirm with the Repairer that all repair work will be carried out in accordance with the British Standard.
A summary of the main points contained within BS AU 159 is shown below.
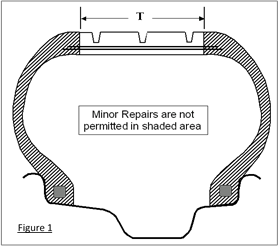
Repair in area ‘T’ only, requiring one of the following:
- Rubber only combination plug patch.
- Rubber only patch and penetration filling material.
Note: Insertion of a tube in a tubeless tyre is not considered a suitable alternative to a permanent repair
Note: Minor surface rubber repairs (i.e. no penetration or ply damage) using penetration filling material only, are permitted anywhere on the exterior of the tyre without limits.
Repairable area ‘T’ defined as percentage of nominal section width of tyre | Maximum diameter of penetration damage at base of injury in area ‘T’ mm (after preparation) | |
---|---|---|
Nominal Section Width mm | % | |
Up to and including 155 | 60 | 6 |
Over 155 and up to 200 | 65 | 6 |
Over 200 | 70 | 6 |
Calculated width values for area ‘T’
Nominal tyre section width | ‘T’ Value mm |
---|---|
125 | 75 |
135 | 81 |
145 | 87 |
155 | 93 |
165 | 107 |
175 | 114 |
185 | 120 |
195 | 127 |
Nominal tyre section width | ‘T’ Value mm |
---|---|
205 | 144 |
215 | 151 |
225 | 158 |
235 | 165 |
245 | 172 |
255 | 179 |
265 | 186 |
275 | 193 |
Nominal tyre section width | ‘T’ Value mm |
---|---|
285 | 200 |
295 | 207 |
305 | 214 |
315 | 221 |
325 | 228 |
335 | 235 |
345 | 242 |
Procedure
1. INITIAL INSPECTION
a) In the interests of safety, if it is necessary to partially inflate the tyre to locate the injury/penetration, proceed with caution in 5 psi increments and do not exceed 15 psi.
b) Remove the tyre from the wheel and thoroughly inspect, both internally and externally.
c) Do not undertake repair if the tyre exhibits any of the following:-
- Inadequate tread depth (legal minimum 1.6mm).
- Splits, cuts, rubber crazing/cracking reaching the casing.
- Casing break-up.
- Previous repairs outside the scope of BS AU 159 unless they are specialist repairs carried out by the original tyre manufacturer.1
- Significant contamination by solvents etc.
- Bead damage, including broken bead core.
- Liner deterioration.
- Secondary effects, e.g. under-inflation/deflation damage or savaging by the point of a penetrating object.
- Exposed cords due to tread wear or sidewall scuffing.
- Tread or sidewall rubber separation.
- Belt separation (radial ply tyres).
1 Tyres with major repairs conforming to the British Standard should be marked internally BS AU 159 adjacent to the repair together with the repairer’s name and identification mark.
2. PREPARATION AND REPAIR
a) Ensure that the tyre is clean and dry.
b) Determine the angle of penetration.2
c) Prepare the penetration channel with minimal use of a rotary mill cutter or similar.
d) Remove all loose and visibly oxidised material, buffing the rubber in the cavity and surrounding area to a suede finish.
e) Clean an area significantly larger than the patch with solvent, removing all contaminants, e.g. mould releasing agents.3
f) Hold the patch in position and mark its outline on the inner liner.
g) Mechanically buff the inner liner to approximately 5mm beyond the marked area, removing any raised ribs and producing a flat, suede finish
h) Remove dust and extraneous material, e.g. wire particles and fluffed cords.4
i) Apply suitable repair material in accordance with manufacturer’s instructions.
2 If the angle exceeds 25º, a two-piece repair system or rubber only patch with penetration filling material may need to be used (refer to manufacturer’s instructions).
3 If buffer liquids (solvents) are used, the area should not be considered buffed.
4 A vacuum cleaner is recommended. Fibrous cloths and compressed air should not be used.
3. GENERAL NOTES
a) Injuries in excess of those shown in the above tables and not having the non-repairable conditions listed in section 1c) should be submitted to an approved major repairer.
b) There is no limit to the number of minor repairs in area ‘T’ provided that repair patches do not overlap.
c) Tyres repaired to BS AU 159 are able to operate at their original speed and load capabilities.
d) The following ‘repair’ methods are not recognised as acceptable:-
- Liquid sealants.
- Plugs applied externally to fitted tyres.
- Inner tubes fitted to tubeless tyres.
- Inner tubes fitted to ‘tube type’ tyres which have sustained penetrations and which have not been repaired in accordance with BS AU 159.
- Temporary repairs.
e) The British Standard does not apply to T-type temporary use spare tyres. 5
5 Temporary spare tyre designed for use at higher inflation pressures than for standard or reinforced (extra load) tyres.
Licence No. 2010ET0033 Permission to reproduce extracts from BS AU 159f :1997 is granted by BSI. No other use of this material is permitted. British Standards can be obtained in PDF or hard copy formats from the BSI online shop: www.bsigroup.com/Shop or by contacting BSI Customer Services for hard copies only: Tel: +44 (0)20 8996 9001, Email: cservices@bsigroup.com
The recovery of used tyres is both an opportunity and a challenge. Used tyres are potentially a valuable resource for reuse, retreading or other recovery processes according to their condition. However, unscrupulous operators have been too ready to shirk their responsibilities. Over the years a body of legislation has built up to address these different issues. This document identifies the principal obligations relating to used tyres in England and Wales and how to comply with them.
The cause of any irregular wear or failure of truck and bus tyres should be thoroughly investigated and rectified. The following factsheets provide pointers as to the likely causes and remedies for most known truck and bus tyre defects.
Regrooving can extend the life of suitable truck and bus tyres by up to 30%. However, only tyres designed for regrooving and marked “Regroovable” can legally be regrooved. It is also a legal requirement to follow the manufacturer’s regrooving pattern.
Applicable Regulations
Construction and Use Regulations 24 and 27 apply. Only tyres identified on the sidewall as regroovable may legally be regrooved. This applies to both new and retreaded tyres. It is also a legal requirement that any regrooving must follow the pattern specified by the manufacturer. If the tyre cords are exposed as a result of regrooving the tyre is no longer legal and must be withdrawn from service.
Basic Principles
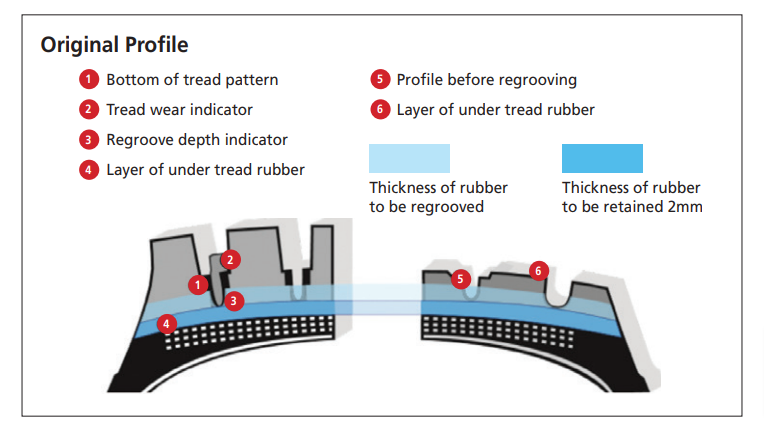
The regrooving operation consists of cutting into the tread of a tyre a tread pattern deeper than the original, so as to prolong the tyre’s useful life. When regrooving, it is of fundamental importance to avoid exposing the upper belts of the tyre, and to ensure that an adequate layer of rubber is left to protect them. Tyre manufactures supply specific instructions regarding the patterns and procedures to follow in the regrooving of tyre treads. These include recommended groove widths and the depth of rubber to remove from the base of the original grooves.
Regrooving should normally be carried out on the entire tread according to the recommended pattern and procedure. However, where a tyre has worn abnormally, it may be possible to regroove just that part of the worn tyre, provided a sufficient portion of the original groove is visible before regrooving. Clearly, this precludes further re-grooving later in the tyre’s life.
Manufacturer’s regrooving patterns
Click on the hyperlinks below to access the manufacturer’s guidance and regrooving patterns.
Bridgestone | Continental | Dayton |
Firestone | Giti Tire UK | Goodyear |
Hankook | Michelin | Pirelli |
New tyre labelling regulations came into force on 1 May 2021
A new EU labelling regulation came into force on 1st May 2021, updating and extending the previous provisions. However, there is no change to the regulatory intent:
to increase the safety, and the economic and environmental efficiency of road transport by promoting fuel-efficient and safe tyres with low noise levels.
The new EU regulation has full force and effect in N Ireland from 1st May. The UK government has indicated its intention to maintain alignment with the new EU regulation in Great Britain. However, new GB legislation to implement this intention is still a work in progress. Consequently, the “old” regulation is still in force in Great Britain.
Until alignment is achieved in Great Britain, focus should be on communicating with the consumer about tyre performance, rather than obsessing with the regulatory small print. The Department for Transport has welcomed the industry commitment to maintain consistency of communication throughout the interim period.
New label
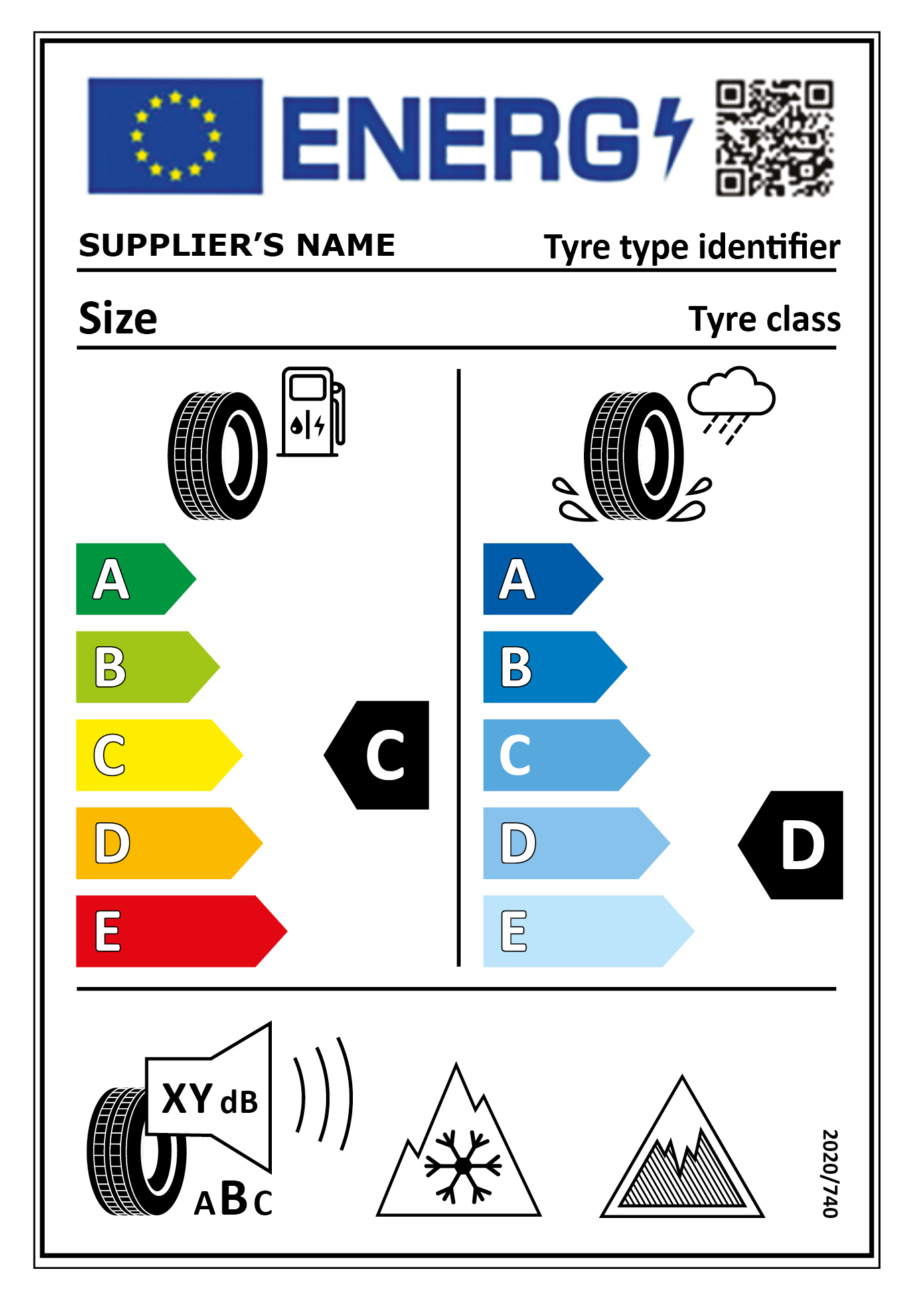
Old label
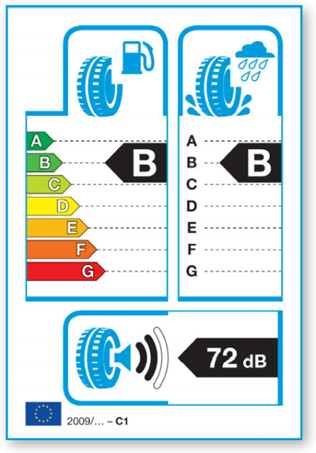
Regarding consumer communication, the new EU regulation introduces extended obligations in relation to the “old” regulation. Only one of the old obligations is repealed by the new EU regulation – that of showing the labelling information on customer invoices. See table below for details.
Tyres with the new label will progressively replace existing stocks showing the old label. In Great Britain and in N Ireland distributors may handle existing stocks in accordance with the “old” regulation. In N Ireland distributors must handle tyres with the new label in accordance with the new EU regulation. In Great Britain distributors may continue to follow the communication requirements of the “old” (ie current) regulation even though the tyre bears the new label.
However, distributors on both sides of the water may find it convenient to adopt the conventions of the new Regulation for all products.
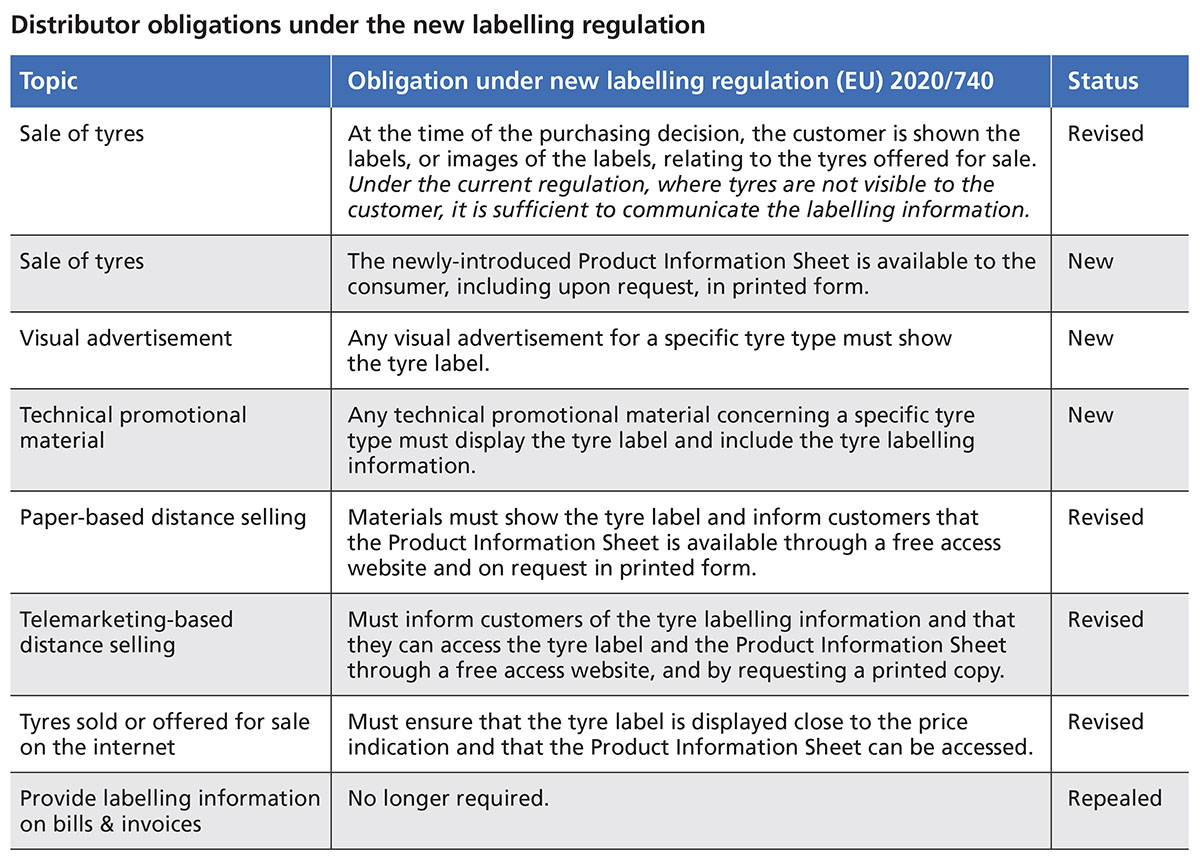