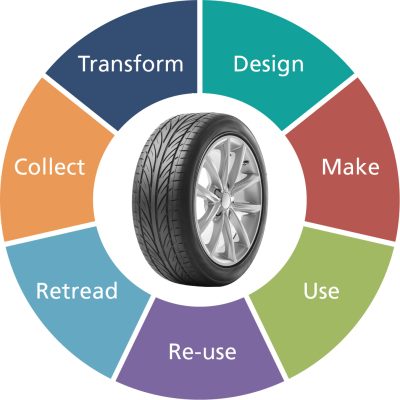
Every year over 50 million tyres are supplied in the UK. BTMA members are committed to further increasing the sustainability of road transport through improved performance at every stage of the product lifecycle.
New products, new markets and new ways of doing business are all subjects of current industry research and innovation.
Tyres are above all else a safety-critical vehicle component. Intense competition and increasingly demanding regulation continue to drive extended functional and environmental performance. This is enabled by cutting-edge research into material technology and advanced manufacturing methods.
Tyre design must achieve a fine balance between multiple performance parameters. Some of these are antagonistic, for example, increasing wet grip reduces tyre abrasion resistance. BTMA members are committed to establishing a robust and representative tyre abrasion test method by early 2024. It is expected that this will support international regulation requiring a minimum standard of abrasion resistance for new tyres. In the meantime, tyre manufacturers are already introducing new product ranges with enhanced wear resistance.
Despite appearances, tyres are a hi-tech composite requiring high performance raw materials to meet the ever-increasing demands on safety, performance and environmental impact. Typically, over a dozen different rubber compounds are used in a tyre, each tailored to its particular location and function.
BTMA members are pursuing the use of recycled, recovered and bio-sourced materials in new tyres without loss of functional performance. Many major manufacturers have committed to producing tyres from 100% sustainable raw materials by 2050. Several manufacturers have already presented tyres with up to 93% sustainable content.
However, progress is time-consuming. Not only must alternative raw materials be developed but the formulation of the tyre itself must often be adapted to accommodate their slightly different characteristics. Switching to alternative raw materials is rarely a straight swap; extensive product testing is necessary in order to respect the imperative of maintaining product safety. Product development cycles are typically 4 years for car tyres and 7 years for truck tyres.
BTMA members have developed alternative plant-based sources of natural rubber to relieve pressure on supplies from rainforest plantations and have launched pilot plants to produce synthetic rubber from biomass. Tyre manufacturers are already using soy bean-based extender oils, silica produced from rice husks and textile reinforcement derived from recycled plastic bottles.
Recycling material from old tyres into new ones is challenging due to the material choices that are imposed by the multiple functional requirements that a tyre must satisfy. The incorporation into new tyres of more than a few percent of rubber from end-of-life tyres adversely affects functional performance, wet grip in particular. Research is ongoing into increasing this proportion but large-scale reincorporation of materials from old tyres into new ones requires the use of chemical recycling techniques.
The pyrolysis of end-of-life tyres offers several pathways to material re-use in new tyres. The char can be processed into recovered carbon black (rCB). However, this can only be used in limited quantities in new tyres due to the adverse effect of the presence of other residual materials. More promising is current research into the use of tyre pyrolysis oil as feedstock for the manufacture of sustainable carbon black. This route offers the potential for much higher rates of reincorporation in new tyres than rCB. Research is also ongoing into the use of the gas produced by tyre pyrolysis as a starting point for the manufacture of sustainable synthetic rubber.
For our position about sustainable raw materials, click here.
For the tyre industry’s roadmap to United Nations Sustainable Development Goals, click here.
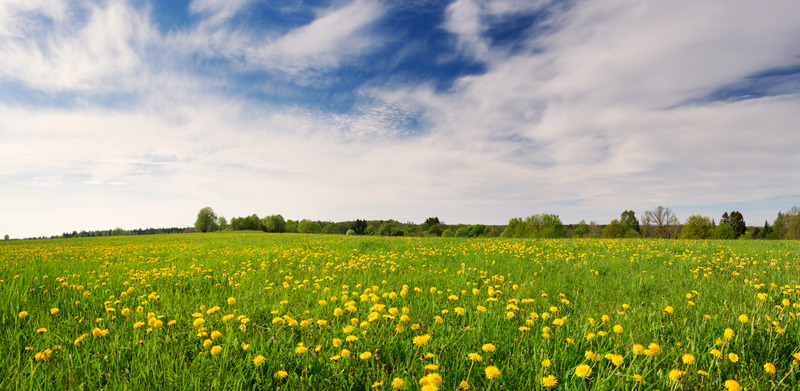
Tyre neglect is widespread: 17% of MOT test failures are tyre-related. Improved tyre stewardship would bring significant improvement to both the environmental impact of mobility and road safety.
Surveys show repeatedly that 25% of vehicles have at least one tyre 25% under-inflated. Over 600,000 tyres and 1.5 million tonnes of CO2 are wasted in the UK every year due to tyre under-inflation.
Highways England report over 3600 tyre-related incidents a year on the strategic road network causing personal inconvenience, traffic disruption and risk to roadside repair personnel. Many of these incidents could be avoided through improved tyre care.
Recognition of the impacts, direct and indirect, of our actions is a first and necessary step on the journey towards improved road safety and increased resource efficiency.
For information on customer choice of replacement tyres, click here.
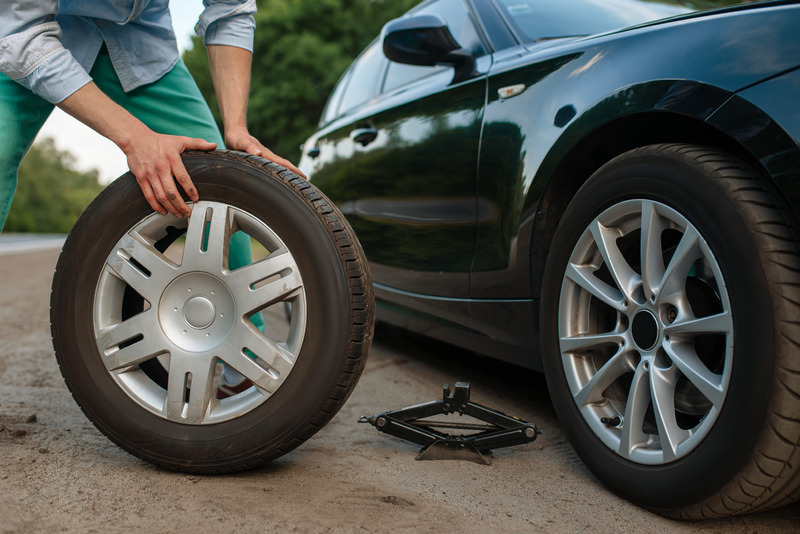
Defra reports that over 5 million salvaged partly-worn tyres are supplied in the UK every year. This represents about 12% of the replacement tyre market. Although this contributes to the circular economy, many used tyres are not suitable for further use; of almost 500 blind purchases of second-hand tyres made by Trading Standards Officers in recent years, 58% did not comply with the minimum safety standard required by regulations.
Demand for second-hand tyres is longstanding and resilient. Market research shows that consumers are principally the young and economically disadvantaged. Those of modest means should not be obliged to compromise on road safety, for themselves or for other road users.
The present market for second-hand tyres is failing to protect the motorist. A better functioning market is needed to satisfy demand with safe product whilst contributing to improved resource efficiency.
For more information on second-hand tyres, click here.
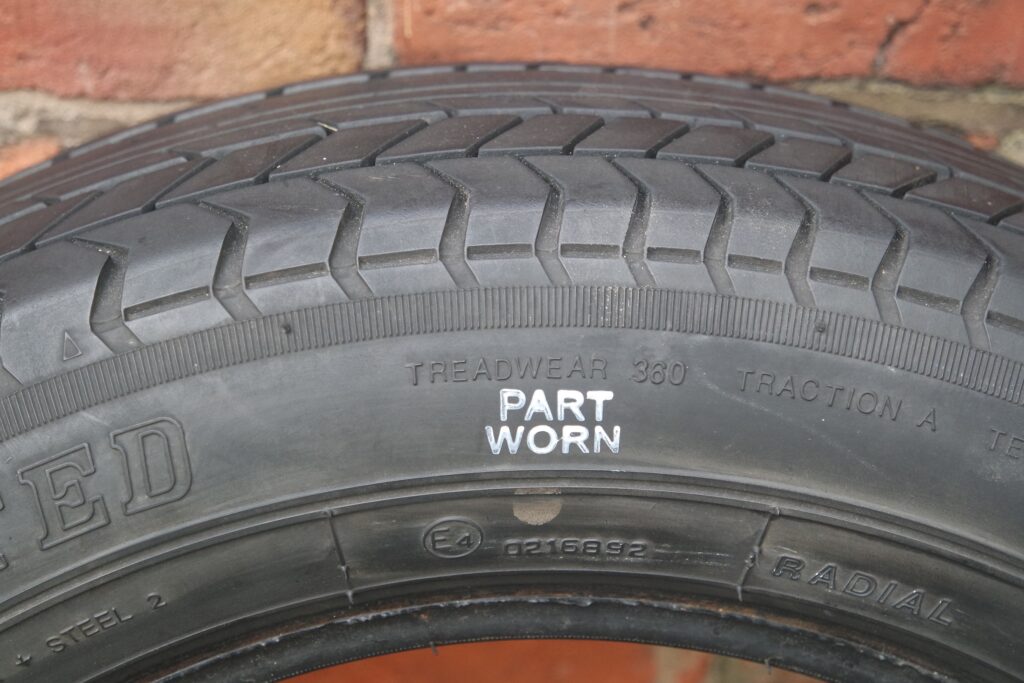
Retreading gives a whole new life to suitable used tyres. However, barely 50% of candidate tyres meet the exacting requirements to be given a second life.
Retreaded tyres are safe: 4 out of 5 civil aircraft land on them. International regulation ensures that retreaded tyres meet the same safety standards as new tyres. In all other respects retreaded tyres offer similar or better performance than the original tyre.
Using retreaded truck and bus tyres delivers three times the resource efficiency and consumes four times fewer tyres than using low-cost single-life tyres. All at the same overall tyre cost per mile.
Over 80% of retreaded truck and bus tyre used in the UK are made in the UK. 85% of the used tyre is re-used in a retread, greatly increasing resource productivity and improving supply resilience.
Truck and bus tyre retreading has the potential for a further 25% increase in market share, reversing the recent losses to low-cost single-life “budget” tyres. This would restore the market share of retreaded truck and bus tyres to its historical level of 45% of replacement tyre sales, save the consumption of 300,000 tyres every year and support over 5,000 UK jobs.
For more information on retreading, click here.
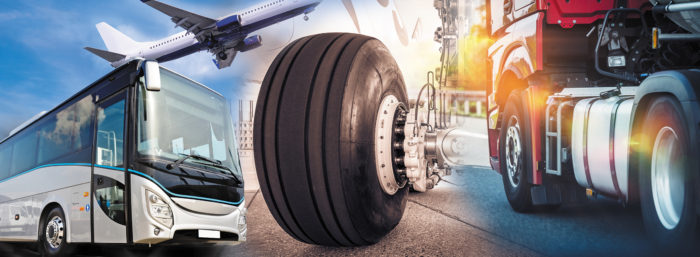