Introducing the New BTMA Brand The British Tyre Manufacturers’ Association (BTMA) has revealed a bold…
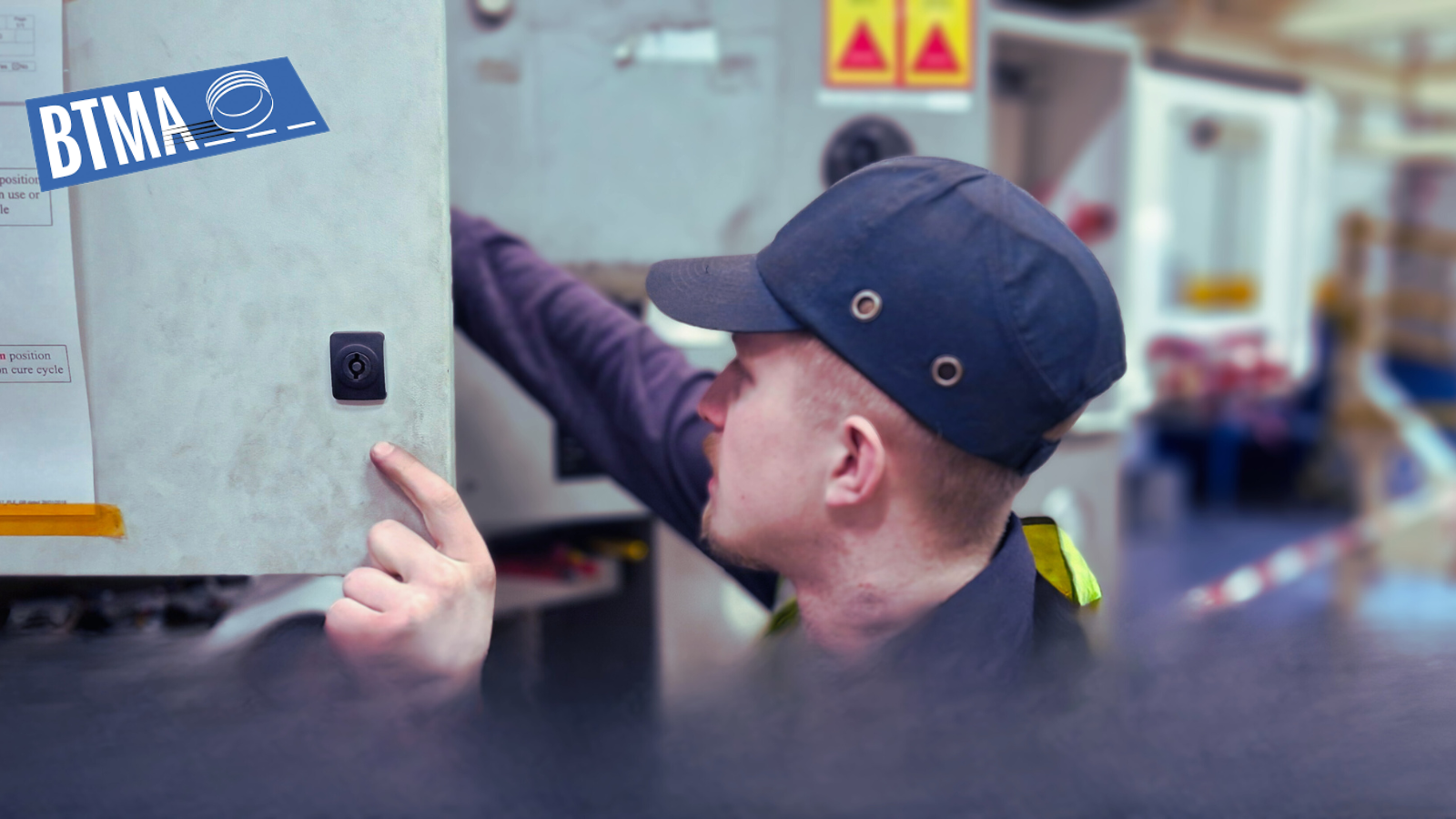
National Apprenticeship Week – From Apprentice to Industry Advocate
Ross Evans’ Journey at Michelin and the Value of Tyre Industry Apprenticeships
Exploring the growth and opportunities within the tyre industry, Ross’s story highlights the importance of apprenticeships for attracting and nurturing young, skilled talent and securing the future of the sector.
Ross, 34, has made a significant mark at Michelin, where he began his career as an apprentice. His story highlights the value of apprenticeships, not only in developing technical skills but in creating a long-term sense of discipline, teamwork, and career progression in the tyre industry.
Ross’s journey into engineering started early. Raised in a family of engineers, he was naturally drawn to working with cars and mechanics from a young age. “I was always hands-on at home, helping with cars and working on small projects around the house,” Ross says. “My dad was an engineer, and there were others in the family too, so it was a natural path for me.”
After completing his electronics course at Stoke-on-Trent College, Ross realised that the theoretical side of education wasn’t the right fit for him. “It was all theory-based, with little practical application, and I wasn’t enjoying it,” he admits. “I’m the type of person who learns by doing, so I decided to look for an apprenticeship that offered more hands-on learning.”
In 2009, Ross joined Michelin as an apprentice, having considered two options: a distribution warehouse job at New Look or an engineering apprenticeship at Michelin. With the support of family members who worked at Michelin and the appeal of the company’s reputation for supporting its staff, he chose to start his career with the tyre manufacturer.
Ross’s apprenticeship was designed to provide a balance of theoretical and practical learning. The first year consisted of four days a week at college, learning core skills such as electronics and engineering principles, while one day was spent at Michelin observing experienced engineers. “In the first year, you’re really just observing and asking questions. You’re learning from the people around you,” Ross explains.
The second year saw a shift to a more hands-on approach, with Ross spending four days a week in the factory working alongside experienced engineers, while continuing his studies one day a week. This is where Ross found his stride. “That’s when I really started to enjoy it. I prefer learning by doing, and the apprenticeship offered just that,” he says.
Michelin’s investment in apprenticeships came at a crucial time. With an ageing workforce and many engineers nearing retirement, the company saw the value in training young talent to ensure continuity and growth. However, it wasn’t without its challenges. While many apprentices like Ross thrived, not all completed their apprenticeships, with some leaving for higher wages elsewhere. “I did think about leaving at one point, and Michelin had to work hard to keep me, but they showed their commitment,” Ross explained.
Ross reflects on how Michelin’s approach to apprenticeships not only prepared him technically but also instilled transferable skills. “It’s about more than just the technical side. It’s about learning how to work as part of a team, developing social skills, and understanding discipline. Michelin’s method of working, the ‘Michelin way’, really shaped how I approach my job today.”
Over the years, Michelin’s commitment to its apprentices paid off, not just in the immediate development of technical skills but in creating a culture where young engineers feel invested in the company’s long-term values. “The company makes sure you feel valued,” Ross explains. “You’re involved in projects from the start, and as you progress, you see how the decisions you make impact the company.”
In addition to technical training, Michelin provided Ross with the opportunity to be part of a £10 million investment in the factory, including the introduction of new systems and technology. “I’ve been part of major changes here, and I’ve seen the business grow from the ground up,” he says. “We’re always looking for ways to improve, and that’s something I’ve learned from my apprenticeship. It’s about embracing change and evolving.”
Now, as a manager overseeing the next generation of engineers, Ross is a strong advocate for apprenticeships. “The apprenticeship programme offers so much more than a qualification. It gives you a chance to develop the skills and mindset to succeed in this industry and beyond,” he says. “The first year can be tough, but it’s worth it, it’s an investment in your future.”
Final Thought of Advice
“For anyone considering an apprenticeship in the tyre industry, it’s a great way to earn a really good wage while building a career that can last 40 years. You’re learning practical, transferable skills that you can use in all areas of life, whether it’s helping a friend with DIY at home or working on your car. The skills you gain in engineering can be applied to so many aspects of daily life. There are so many opportunities to learn, and it’s a career that will keep you engaged and growing,” Ross advises.
Ross’s story is a reminder that apprenticeships are a vital part of the tyre industry’s ongoing development. By fostering a workforce that is not only technically skilled but also aligned with a company’s values, apprenticeships create a future-proofed pipeline of talent. For young people looking to join the industry, it’s a proven route to a rewarding career.